

Mecedes Trucks
Mercedes-Benz has been producing trucks since 1896, making it one of the oldest manufacturers in the world. Today, Mercedes-Benz trucks are built in various locations around the world, including, Brazil, Argentina, and South Africa. The company is known for its high-quality, reliable trucks that are used in a variety of industries from construction to transportation.

Mercedes-Benz History: the Wörth Truck Plant in Germany Largest Truck Factory in The World
Back in 1963, then Daimler-Benz AG was establishing a new commercial vehicle plant in the German district of Wörth.
Fifty years later, the largest truck assembly plant on the planet being hosted in Wörth, where an army of more than 11,500 workers are building trucks sporting the (large) three-pointed star.We are talking about models like the Actros, Arocs, Axor, Antos and Atego, but this is where the Mercedes-Benz Special Trucks division is also based, where the zombie-proof Zetros, the Econic and the legendary Unimog are also manufactured.All in all, more than 100,000 on and off-road giants are currently made in Wörth each year.Initially, when former Daimler-Benz AG had purchased an industrial site comprising of about 1.5 million square meters from the district of Wörth, neat Karlsruhe, the initial plan was merely to build an engine factory there and only about 100 workers were to be employed.Even so, around 22,000 cabs rolled off the production line during the first year of operation. Over the years, the site saw a gradual transformation from the original plans into what it is today, the largest plant of its kind in the world.
Acquisition of the premises was hardly spectacular, meriting a few marginal lines in the Annual Report of 1960: “In the Wörth area near Karlsruhe industrial premises have been purchased that lie favourably close to the South German parent plants and on which construction of a production facility for major assemblies will begin in the near future.” And that was about the only mention at the time of Wörth, the plant that has long since become the largest truck plant in Europe today.
On 27 July 1960 the Supervisory Board had authorised the acquisition of premises covering an area of 1.5 million square metres, although the acquisition remained largely unmentioned until the Annual Report of 1962: “Cabs for all truck models in the Mannheim and Gaggenau programmes are to be built at a new production facility, scheduled for completion in late 1963,” ran the succinct report. Then another year passed before the Annual Report of 1963 offered an idea of the scale of the new plant. “At Wörth a. Rh. we have at our disposal sufficient reserves of real estate to enable us to create the facilities necessary to increase in the future our commercial vehicle production, with a view to expanding and improving the structure of our operations.”
What was being referred to here was a restructuring of truck production – at the time restricted to Mannheim and Gaggenau – in line with passenger car production (where responsibilities were shared between Sindelfingen and Untertürkheim), with central assembly taking place in Wörth, and Mannheim and Gaggenau taking care of supplying the major assemblies (engines from Mannheim, axles and transmissions from Gaggenau).
The aim here was to achieve cost benefits generated by highly rationalised large-scale production, which in turn would serve to boost overall truck sales considerable and ultimately secure for the company nothing less than the leading position worldwide for trucks of over six tonnes GVW. The Group’s strategy at this time was to concentrate on the luxury-class passenger cars and to establish a presence where trucks were concerned as a full-range and mass producer.
This realignment of commercial vehicle strategy had become necessary as a result of the discontinuation of CKD (completely knocked down) deliveries to Brazil, India and Argentina; thus the only way to ensure utilisation of capacities in domestic plants was by developing new markets. But the key to success on the international market was Wörth. For Wörth meant large-scale production across the board and thus cost reductions that would benefit competitiveness on the global market.
The Annual Report of 1965 put it as follows: “By developing the Wörth plant, truck production will be brought into line with the same principle that has proved effective for many years in passenger car production – the separation of major assembly production and vehicle assembly. This approach means that production can be rapidly adapted to meet market requirements and that greater cost benefits of large-scale production can also be realised.”
It was a double premiere that was staged at the new Wörth plant on the River Rhine on July 14, 1965. Not only did the first completely assembled truck come off the production line, decorated with flowers and attended by the plant management. The launch of the Mercedes-Benz LP 608 also marked Daimler-Benz’s entry into the light-duty class, a big step on the company’s way to becoming a full-line producer.
In both respects, things went extraordinarily smoothly. In its first two years in production, the LP 608 cab-over-engine truck reached an impressive market share of 45 percent with a total of 10,000 units produced. It was the originator of the LP truck class ranging up to the LP 1113, and this series was to remain in production for a good 20 years and record a total volume of some 200,000 units.
​
​

Europe’s largest truck plant in next to no time
The Wörth plant, in its turn, being the central European production facility for trucks, developed into Europe’s largest truck plant in next to no time and continues to occupy this rank today with production figures that speak for themselves: since July 1965, the Wörth plant has turned out about 3.3 million trucks.
It all began on a much more modest scale and with a workforce of less than 100 employees. Wörth began producing truck cabs as early as October 1, 1963. Initially, however, the plant merely supplied primed cab shells for completion at the traditional locations, Gaggenau (heavy-duty trucks) and Mannheim (medium-duty trucks). In the first year, the Wörth plant produced over 22,000 cab shells. From December 1964, in-house manufacture was stepped up in that the interior equipment was also installed and the cab shells were painted at the new plant, starting with the cabs of the 314 model.
Centrally located between Mannheim and Gaggenau
Even geographically, Wörth seemed predestined to adopt the role as central plant. The new location, occasionally also referred to as Wörth Island, was ideally situated between the plants in Gaggenau and Mannheim, which had reached the limits of their combined capacity – 40,000 trucks annually – during the period of the economic miracle in Germany. The new plant, located in a former loop of the River Rhine, was required to overcome bottlenecks. The ground-breaking ceremony on the 1.5 million square kilometre site was held in March 1962.
It had been impossible to foresee the enormous development that would take its course on the premises acquired from the municipality of Wörth back in 1960. Initially, nothing more than an engine plant had been planned. But then in 1963, Daimler-Benz restructured its production activities, concentrating engine and bus production in Mannheim, and Unimog, axle and transmission production in Gaggenau.
It was not until 1964, however, that the final decision was made to unite all truck production and final assembly activities in Wörth. Other facets of the division of labour within the company at the time were as follows: Mannheim would not only continue producing truck engines but also retain bus production; Düsseldorf was to concentrate on all van models up to four tonnes (later up to six tonnes); Berlin was to assemble complete passenger car, truck and industrial engines and supply vehicle parts; Sindelfingen manufactured passenger cars, and Untertürkheim produced a diversified range of engines; and Gaggenau supplied axles, transmissions and individual components.
Full capacity utilisation reached as early as 1969
Initially the Wörth plant had been constructed for an annual capacity of 48,000 trucks. This volume was reached as early as 1969. Despite the first minor post-war recession in 1966/67, everything ran like clockwork: 800 trucks left the factory in 1965. Production of the LP 608 had been relocated completely from Mannheim to Wörth by the end of that year. Production of medium-duty trucks and CKD (completely knocked down) shipments to assembly plants all over the world began in 1966.
What was once conceived as an engine plant was now itself the motor for the industrialisation of the commercial vehicle business. A glance at the export quota for the domestic plants reveals the extent to which exports were growing during the period: export figures for 1960 were 35.8 percent, rising to 41.7 percent in 1966 and 47.2 percent by 1969.
With the addition of the administrative building, training workshop and staff restaurant, the plant was gradually completed, with the new assembly hall at its heart. At a length of 750 metres (today 1,000 metres) and a width of 50 metres, this was ranked as one of the largest automotive assembly halls worldwide. The fact that both series were produced on one and the same line was seen at the time as a drawback, but it would ultimately prove a blessing. Production was extremely flexible from the very start. Although trucks were not given names at the time, commonly used designations such as “light-duty Wörther” or “heavy-duty Wörther” made clear reference to the vehicles’ origin.
Next target: 100,000 units annually
From 1969 onwards, Daimler-Benz raised the capacity of the plant step by step. The aim was to produce 100,000 units annually. The factory was extended twice until this target was reached – with exactly 105,200 units coming off the production line in 1975. Long before this point in time, Daimler-Benz had relocated the replacement parts warehousing facilities from Gaggenau and Mannheim and concentrated all relevant activities at the central parts warehouse in Wörth, which started operations in 1972. From 1973, Wörth produced the heavy-duty New Generation trucks which had been systematically designed according to the modular principle. Ten years after production start-up, the 500,000th truck left the plant – by which time around 8,700 people were employed on the island in the River Rhine.
All the while, the proportion of plastic components in motor vehicle manufacture had been rising continuously. It was therefore only logical for Wörth to launch activities in this sector as well. The job of moulder was added to the wide spectrum of professions represented at the plant when, in 1977, Wörth assumed responsibility for the production of plastic components for both passenger cars and trucks. The production of aerated-plastic parts for passenger cars also migrated from Sindelfingen to Wörth.
In the 1980s the New Generation was replaced by the NG 80 and the oldest generation of vehicles from Wörth was discontinued. From 1984, the light-duty LP vehicles were replaced by the LK (Light Class) series with permissible gross weights between 6.5 and 13 tonnes and serving this segment with as many as ten basic models, from the 709 through to the 1320. Distinguishing visual features of the new series were slanting side windows – a design first introduced on the TN vans.
Four years later, the NG 80 models in the heavy-duty class were replaced by the legendary SK series, now also with slanted side windows, which remained in production as the New Generation’s grandchildren until 1996. In was at this time, too, that the parts warehouses in Wörth and Sindelfingen gradually reached their limits of capacity. As a consequence, the entire replacement parts business was relocated to a new central parts warehouse in Germersheim near Wörth, which entered service in 1989.
​

Manufacturing more flexible than ever
Production also changed fundamentally. Conventional automating concepts were no longer suitable for coping with the increasingly complex tasks (permanently growing number of variants and fluctuating unit figures). Under the slogan “Body-in-white production 2000″, a facility that permitted maximum integration was built in 1992 for the welding of all cab versions. The idea of a flexible body-in-white production facility had been born.
The procedures for fitting out the cabs also proved capable of improvement. Optimized production processes and material flows characterized the newly organized unit, which started operations – more effectively and more flexibly than ever before – in 1995.
Change-over to Actros production in record time
This created the best possible conditions for the start of the new Actros heavy-duty truck, which followed in the tracks of the SK in 1996. The change-over of production facilities to this heavy-duty truck, newly designed from the ground up, was completed in record time. But that was not all. In 1997, the LK and MK series were replaced by the new light-duty and medium-duty trucks from the Atego series. In 1998, the Atego line-up was complemented by the addition of the heavy-duty Atego – a combination of Actros chassis and Atego cab.
From 2002, the Wörth plant also produced the new heavy-duty Axor truck, designed for particularly high payloads in medium-duty long-distance transport as well as in heavy-duty short-radius distribution. Also, in August 2002, Unimog production moved from Gaggenau to Wörth. At the same time, the plant prepared itself for production start-up of the second-generation Actros (from January 2003); that same year, Wörth also assumed responsibility for the production of the Econic, the municipal specialist vehicle. The third member of the family produced at Wörth was the off-road specialist Zetros, which Mercedes-Benz unveiled at the IAA in 2008.
Capacity for over 110,000 units
Today, at peak periods some 110,000 complete units come off the assembly lines of the Wörth plant annually, now enlarged to an area covering 2.4 square kilometres and employing over 11,000 people. In the record-breaking year of 2008, for example, the number of trucks built – in what is an extremely complex production process – totalled 113,000. For the Actros, construction Actros, Axor and Atego models alone there are around 500 cab designs and more than 2,400 special variants.
It helps, of course, to have key suppliers and their manufacturing facilities located directly on plant premises. The Wörth industrial estate covers an area of approximately 5,000 square metres and accommodates half a dozen companies which do their manufacturing on site (e.g. seats and bunks) before delivering directly to the production line.
In total the plant works with approximately 1000 suppliers. Around half of all parts are supplied either “just in time” or “just in sequence”. Work on the production line has changed radically over the years. Today the various groups in the production process organise every aspect of their work themselves, including scheduling of holidays. Employees across all shifts manage their individual working times at the site, placing fundamental importance on transparency. Large displays keep each group involved in production constantly up to date regarding agreed objectives such as quality key performance indicators, audit results and the number of work days lost due to illness.
Robots of astonishing flexibility
Another symbol of optimised flexibility is the plant machinery – for example, the robots that are used in body-in-white cab production. Each production cell can build any cab from the extremely broad range in any sequence. The individual components are supplied by driverless transportation systems – making this process unique in automotive construction worldwide.
Since 2007 the plant has no longer been known simply as “Werk Wörth” but as “Mercedes-Benz Wörth”. At the Group’s extraordinary general meeting the decision was taken to rename the plant as part of the renaming process from DaimlerChrysler AG to Daimler AG. Henceforth all production locations turning out components or vehicles for the Mercedes-Benz brand now traded under the Mercedes-Benz name. At the same time as the plants were renamed, the truck division at Daimler AG also changed its name: the Mercedes-Benz brands, Freightliner, Western Star, Thomas Built Buses and Mitsubishi Fuso were all subsumed under the Daimler Trucks (previously: Daimler Truck Group).
Daimler Trucks now intermeshed development and production operations closer than ever. For Mercedes-Benz Wörth this meant the setting up of a new Development and Test Center (EVZ), which began operations in 2008. The Group invested around
80 million euros in the new facilities, which comprised three elements: an indoor test area with numerous rough and potholed tracks and 14 different track profiles, a function testing area in the form of a test track, and thirdly a workshop area and office complex. In total the new EVZ employed a workforce of around 300 people.
​

Attractive offers for all truck needs
Although the work of the Development and Test Center takes place largely out of public view, this does little to diminish the fundamental openness and friendliness of the plant itself. Visitors still come in their thousands to take guided tours of the plant. And an even larger number of visitors head for the Customer Center to collect their new truck. The former “self-collection hall” has long since developed into a state-of-the-art Customer Center, where customers can not only collect their new trucks but also receive instruction about its engineering.
For some time now the Center has also offered drivers and visitors special truck seminars and driver training courses. Although the themes focus mainly on safe and economical driving, training is also available on specific themes relating to the motor vehicle and transportation industries. Since 2009 Wörth has also become a venue for further training courses, which truck drivers are now regularly required to attend in line with the law on professional driver training.
Application Information Center – a globally unique facility
Dedicated to various individual sectors of industry, the Application Information Center (BIC) opened its doors in 2000 – the only institution of its kind worldwide that not only provides customers with sound advice but also permits direct comparison of many complete packages for individual industrial sectors on site. Numerous different Actros, Atego, Axor, Econic and Zetros models complete with superstructures and equipment are available here for comparison and testing.
​
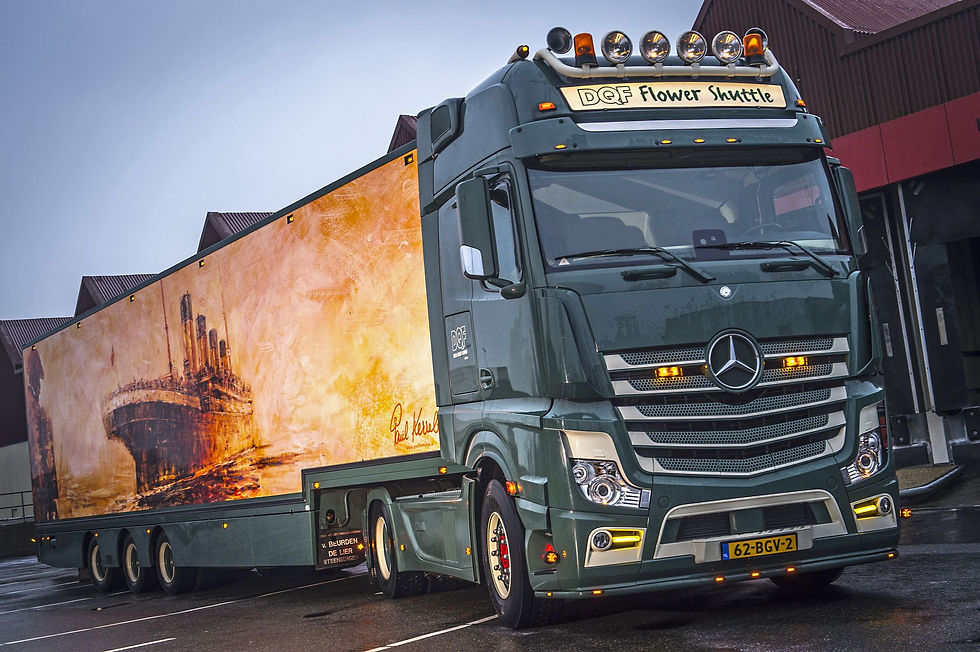
The new shape of efficiency.
The new Actros L with the ProCabin
Design that pays off: The Actros L with ProCabin combines fuel-saving aerodynamics, comfort and safety – for even more efficiency on the road.
Highlights
Working and living under one roof.
Because every litre of fuel counts on long journeys: With its innovative cab design, the Actros L ensures even better aerodynamics. It is only sparing in terms of consumption – not in terms of safety and comfort. Numerous assistance systems give you that good feeling of being on the road safely. And because relaxed driving also includes relaxing breaks, the interior with its many comfort functions ensures rest and relaxation.
Simply efficient: the striking aerodynamic design of the ProCabin cab. It reduces the consumption of the Actros L by up to 3% compared to its predecessor1. Good looks that pay off – every kilometre of the way.
Cost effectiveness
Efficient at first glance.
The 80 mm longer front end enables a completely new, even more aerodynamic design. Every detail of the ProCabin has been designed to divert the front air flow with as little drag as possible. The result: an efficiency increase of up to 3%1 compared to its predecessor. In combination with the economical 3rd generation OM 471 engine, this is the right choice for greater efficiency on long journeys. In this process, the engine generates plenty of output. Thanks to Top Torque, a further 200 Nm is available at the touch of a button – helpful on hills and when accelerating, e.g. when approaching the motorway.
Exterior
Good lighting. Better view.
The most important sensors at the wheel are your eyes. That’s why the Actros L makes no compromises when it comes to lighting. All lighting functions feature LED technology. Matrix LED headlamps are available as an option for even better lighting performance. This gives you a clear view from behind the wheel – and everyone else an impressive sight.
Comfort
Everything at a glance: Multimedia Cockpit Interactive 22.
The secondary display in the Multimedia Cockpit Interactive 2 ensures an even better overview. You can use the touchscreen or switch panel to quickly and intuitively manage climate control, navigation, telephony, infotainment and more. You can also keep your eyes on the road and relay settings and commands via voice control.
Full power. Intelligently put on the road.
Comfort meets efficiency: Predictive Powertrain Control is continuously supplied with information about the route by the navigation system. At the touch of a button on the steering wheel, the system knows where you want to go. It can release the throttle, accelerate and select the optimum gear in conjunction with PowerShift Advanced.
Almost like in a motorhome: SoloStar Concept.
It’s best to drive relaxed. The optionally available SoloStar cab concept impresses with its genuine living space character: with a seating corner providing ample legroom, a table with a cutlery compartment, alternative seat covers and much more. Because your truck becomes your second home, especially on long journeys.
Safety
Uncompromising safety: assistance systems.
Safety is on board. The Actros L doesn't leave you alone at the wheel. Numerous safety assistance systems are there to help you. After all, you’re on the road in a truck from Mercedes‑Benz Trucks – it goes without saying that you feel safe behind the wheel.
Digital services.
Give yourself some digital help with vehicle management to make the processes surrounding your truck more profitable: with smart services like Mercedes‑Benz Trucks Uptime, Fleetboard, TruckLive and the customer portal My TruckPoint for Mercedes‑Benz Trucks. For improved maintenance planning, shorter workshop visits, greater transparency on the road and dynamic route planning using real-time traffic data. As an aside: even our Mercedes‑Benz Trucks Service24h is even faster in the event of a breakdown if it can access the digital data of the Actros L.
​
​
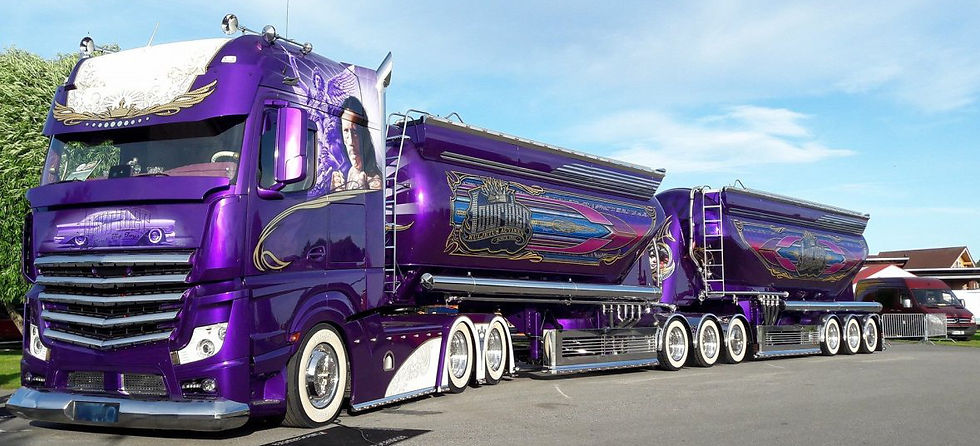
The Actros .
Ready to redefine the standard.
A truck ahead of its time. The Actros meets the continually growing demands in heavy-duty distribution haulage more effectively than ever. With enhanced efficiency. With unique comfort. And with exemplary reliability.
To this end, we have equipped it with pioneering technical innovations which markedly reduce fuel consumption, further boost vehicle use and safety and offer drivers even better support in carrying out their work in the field of heavy-duty distribution haulage. Unique, future-oriented connectivity and the harmonious interaction of intelligent assistance systems are additional defining attributes of the Actros, on the basis of which we are able to offer you an excellently configured, highly efficient vehicle for practically any type of operation in heavy-duty distribution haulage.
Advantages at a glance.
-
Greater comfort thanks to the Multimedia Cockpit1, MirrorCam2 and the electronic parking brake
-
On request for certain Actros Active Drive Assist 23,4,5 for active stress relief for the driver and for increased driving safety
-
Simple handling and operation of the most diverse vehicle and body functions via the secondary Multi-Touch-Display6
-
Mercedes-Benz Truck Navigation6,7 and Traffic Sign Assist3,6,7
-
New key, convenience central locking system
-
Wide range of seats designed to maintain occupant fitness, with numerous adjustment options
-
Active Drive Assist 24 for enhanced driving comfort and high efficiency
Your workplace in the Actros.
Comfort and work in perfect harmony.
Comfort is more than just luxury. It is our answer to the need for higher standards in heavy-duty distribution haulage, providing for pleasant working and driving conditions.
Modern, ergonomic, practical, motivating and not least of all efficiency-boosting. Whether you are a driver or fleet operator, we're convinced you'll be delighted by the workplace in the Actros. It offers the driver the best possible working and driving conditions. And through intelligent networking with headquarters and logistics processes it contributes to even better performance.
Efficiency.
Economical to the core.
The Actros stands for reliable, fuel-saving vehicle technology, lower costs and higher profitability. In short: greater efficiency. Low fuel consumption is a crucial contributory factor to economic efficiency. This is a virtue that the Actros has demonstrated in daily use.
The Actros now boasts additional fuel savings of up to 5%. This results, for example, from further optimisation of the drivetrain, the use of MirrorCam2 and from enhanced Predictive Powertrain Control, which is now also able to contribute to fuel savings on country roads and highways.
​
​
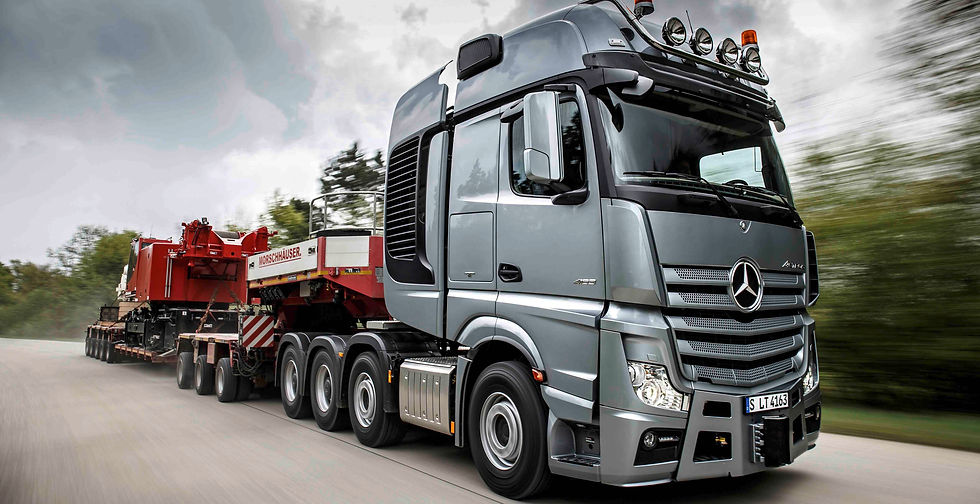

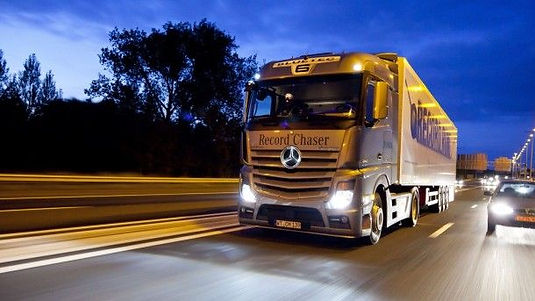
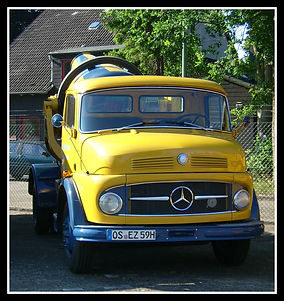

Section Title
Every website has a story, and your visitors want to hear yours. This space is a great opportunity to give a full background on who you are, what your team does and what your site has to offer. Double click on the text box to start editing your content and make sure to add all the relevant details you want site visitors to know.
If you’re a business, talk about how you started and share your professional journey. Explain your core values, your commitment to customers and how you stand out from the crowd. Add a photo, gallery or video for even more engagement.